Full Costing: Definition, Pros & Cons
When running a small business, it’s vital that you ensure you’re keeping everything in order and in check and this is doubly important when it comes to your inventory costs.
There are a number of different ways to record your inventory costs. Some are quick and easy, but somewhat surface level and others are more in depth and detailed.
One such way to record your inventory costs is through a method known as full costing. But what exactly is full costing? And how can it help you?
Read on as we take you through a full definition of full costing, and list the pros and cons so that you can make an educated decision on how you will record your costs.
Table of Contents
KEY TAKEAWAYS
- Full costing is a method of accounting that assigns all manufacturing costs to products.
- The main goal of full costing is to accurately track the cost of each product.
- Full costing works for both internal decision-making and financial reporting.
- Whether or not full costing is the right method for your business will depend on your specific needs and goals.
What Is Full Costing?
Full costing is a more detailed way of recording inventory costs than absorption costing. It records all the costs directly associated with making and selling a product, not just those that can be conveniently linked to it as an expense.
If you adjust your accounting system to implement full costing, rather than using absorption accounting, you will see exactly how much raw materials, production overhead and other costs are directly attributable to each unit of inventory.
In other words, you’ll see precisely what it costs you to make and sell each unit of inventory. This information helps you monitor your performance more effectively and take action if there are any anomalies in your figures.
Keep reading to understand more about why businesses change from absorption accounting to full costing and see a worked example of how it affects transactions.
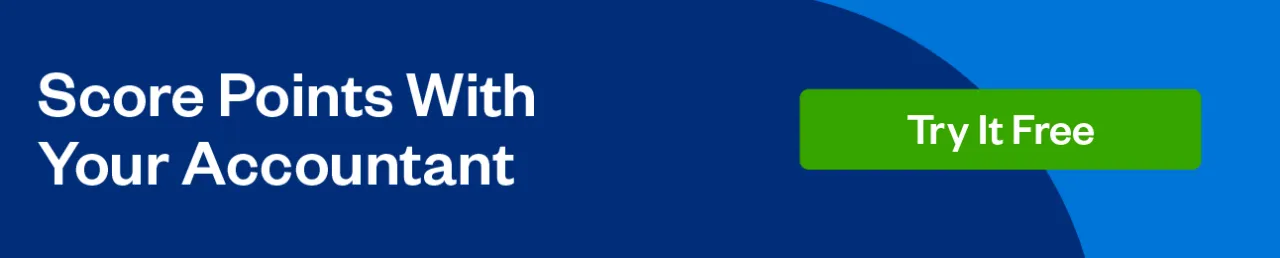
Components of Full Costing
In order to understand full costing, it’s important to know the different types of manufacturing costs involved.
There are three main types of manufacturing costs:
Raw Materials: These are the materials needed to create a product.
Labor: This includes all the direct and indirect costs associated with labor, such as wages, benefits, and training.
Overhead: Overhead costs are all the indirect costs associated with running a business. i.e., rent, utilities, and insurance.
Full costing assigns all of these manufacturing costs raw materials, labor, and overhead to products. This means that each product has its own “full cost” which is the total cost of creating that product.
Full costing is not the right method for every business. Whether or not it’s worth the extra effort will depend on your specific needs and goals.
Here are some factors to consider when deciding whether or not to use full costing:
1. The complexity of your manufacturing process. If you have a simple manufacturing process, full costing may be more trouble than it’s worth. However, if you have a complex manufacturing process with many different types of costs, full costing can be very helpful.
2. The competitiveness of your market. If you’re selling products in a highly competitive market, full costing can help you price your products more accurately.
3. Your financial reporting requirements. In some cases, you must use full costing for financial reporting purposes.
4. Your need for accurate data. Full costing provides accurate data that helps with decision-making. If accuracy is important to you, full costing may be worth the extra effort.
5. Your inventory management goals. Full costing can help you track inventory more effectively and identify areas where costs can be reduced.
It’s important to track your income statement to make sure you don’t exceed your actual costs. Your financial statements make it easy to focus on period costs and operating expenses. Be sure the costs on balance sheets are in order, as well.
Your balance sheet is a vital component in tracking overhead expenses and other product costs. If you need help meeting your inventory goals, use FreshBooks. It has essential tools that make it easy to manage inventory.
You can also use it for your cost accounting report and other cost report items. Accurate cost times are equally vital to your operations.
Advantages of Full Costing
There are several advantages to using full costing in your business:
1. It provides accurate data for decision-making.
2. It’s required for financial reporting in some cases.
3. It can help you price products more accurately (selling price).
4. It can help you identify areas where costs can be reduced.
5. It can help you track inventory more effectively.
Full costing plays a crucial role in operational efficiency. You can track your production costs and cost of materials. Both are important direct costs that you need to know.
But full costing also has some drawbacks that can skew your profit level. Let’s look at some of the cons of full costing to give you a better understanding.
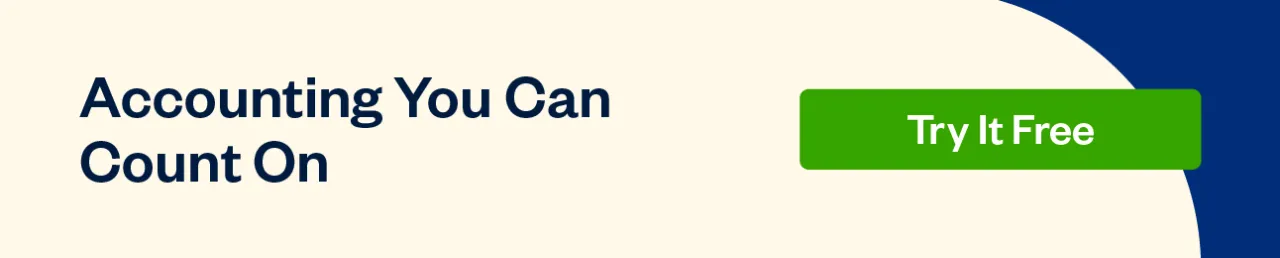
Disadvantages of Full Costing
While full costing has many advantages, there are also some potential disadvantages to consider:
1. It can be time-consuming and complex to calculate full costs.
2. It may not be necessary for businesses with simple product lines.
3. It may not be the best method for decision-making in all cases.
4. It can lead to over-absorption of costs in some cases.
5. It may give you a false sense of precision.
True cost accounting is absolutely vital to your success. Depending on your business model, you might not get the accurate costs per unit you’d hoped for. As such, it’s important to pay attention to costs. If you need to, hire a professional who can help you gain an accurate assessment of input costs.
Full Costing vs Variable Costing
Full costing and variable costing are two different methods of accounting. They both have their own advantages and disadvantages, and they’re best suited for different types of businesses.
Here’s a quick overview of the main differences between full costing and variable costing:
1. Full costing includes all manufacturing costs. Variable costing only includes direct materials and direct labor costs.
2. Full costing is more complex than variable costing.
3. Full costing is often required for financial reporting in many cases. Variable costing is never required for financial reporting.
4. Full costing can be more accurate than variable costing, but it can also lead to over-absorption of costs in some cases.
5. Variable costing is simpler than full costing and may be a better option for businesses with simple product lines.
Example of Full Costing
Let’s say you manufacture widgets. Each widget costs $5 in direct materials, $10 in direct labor, and $2 in overhead costs.
If you use full costing, each widget will have a total cost of $17. If you sell the widget for $17, you will break even.
If you use variable costing, each widget will have a total cost of $15. If you sell the widget for $15, you will make a profit of $2 per widget.
As you can see, full costing can impact your profitability. In this example, full costing would result in a break-even situation, while variable costing would result in a profit.
Summary
Full costing is the more accurate way to measure your costs per unit of product. It takes into account more costs than standard absorption accounting. In an ideal world, you would use full costing to calculate your cost of goods sold and your gross margin.
However, because inventory is an asset, it’s generally easier to calculate COGS using absorption costing. The downside is that you end up with a fuzzy picture of your real costs.
When you implement full costing, you see the actual costs associated with making and selling inventory. This lets you monitor your performance more effectively and take action if there are any anomalies in your figures.
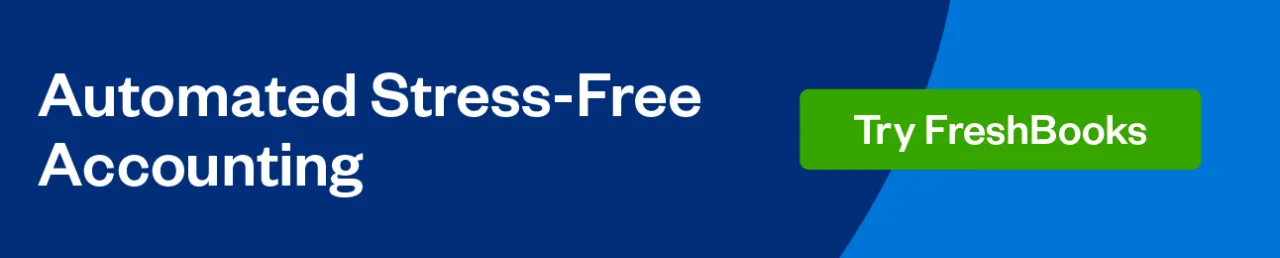
FAQs About Full Costing
To calculate full cost, you need to add all manufacturing costs together. This includes direct materials, direct labor, and overhead costs.
Absorption costing and full costing are two different methods of accounting. They both include all manufacturing costs in the cost of goods sold, but they have different purposes. Absorption costing is typically used for financial reporting. Full costing is typically used for decision-making.
The full cost principle is the accounting principle that requires all costs to get included in the cost of goods sold. This includes direct materials, direct labor, and overhead costs. The full cost principle is important because it gives you a more accurate picture of your manufacturing costs.
Full cost pricing is important because it ensures that all of your costs are covered. This includes direct materials, direct labor, and overhead costs. If you only price based on variable costs, you may not be able to cover your fixed costs. Full cost pricing can help you avoid this issue.
You should use full costing when accuracy is important to you and you need to track all manufacturing costs. You should use the variable costing method if you have a simple product line and you want to keep your accounting as simple as possible.
Share: