What Is Construction Takeoff & How to Do It?
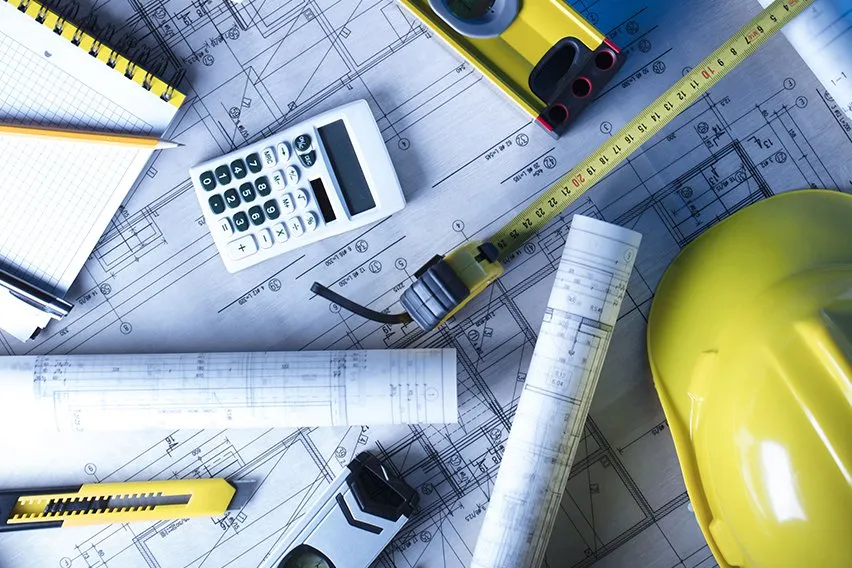
An accurate construction takeoff is essential for budgeting for your construction project. Let’s break it all down
Most people in the construction business will have come across the term “construction takeoff” in their time. It’s an industry term that helps you to estimate the costs of a construction project.
In this guide, we’ll define the term. Then we’ll do a short tutorial on how to do a construction takeoff for your project.
Here’s What We’ll Cover:
How to Do a Takeoff Step By Step
What Is Construction Takeoff?
Construction takeoff is also known as material takeoff (MTO).
The core principle is to calculate the cost of each material individually. You sum it up to get the construction takeoff of the project budget.
In literal terms, the estimator needs to “takeoff” the essential materials from a project blueprint. Calculate the cost of them. That will be the construction takeoff.
An accurate material takeoff is how you get accurate costs for your project overall. Accurate costs means better money management and return on investment.
There is construction takeoff estimating software that can help with this process. But at the heart of it, it’s just an itemized budget of material costs. Nothing too complicated.
I think the most complicated thing about this topic is all of the names!
“Takeoff”. “Material takeoff”. “Construction takeoff”. “Construction material takeoff”. Just know that these all mean the same thing.
If you see “takeoff” attached to a specific material, then that is a specific itemized item in the budget. For example, the estimated cost of the lumber will be labeled “lumber takeoff” on a construction takeoff document.
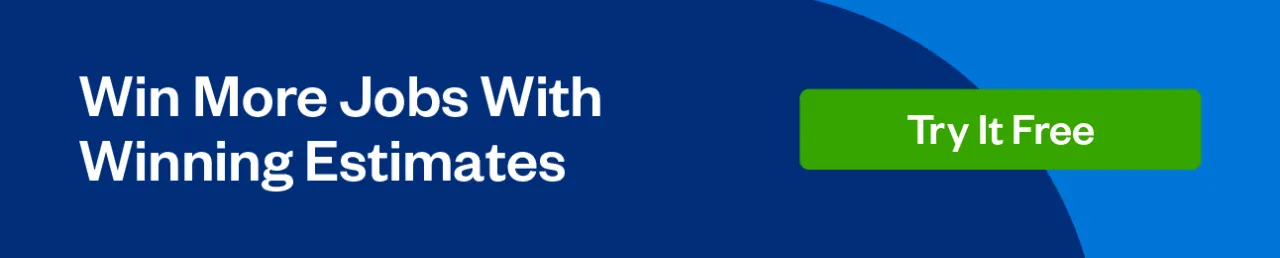
How to Do a Takeoff Step By Step
1. Make a List of Materials Required for the Project
Get to the nitty-gritty. This means all large materials.
Raw materials include:
- Steel
- Lumber
- Sand
- Concrete
Manufactured or prefabricated materials could include:
- Piping
- Electric cables
- Light fixtures
- Glass windows
- Roofing
- Cladding
The material list you need to complete the project should be on your blueprints/construction drawing.
Note that you don’t need to itemize every screw and nail. Doing a construction takeoff is already taxing! Don’t make it harder for yourself. The comprehensive list on your project plan is enough to go off. Complex projects will have a long list of materials that need quantifying. You want detailed takeoffs but not mind-numbingly so. Don’t punish yourself by going too granular.
2. Define the Quantity of Each Material
Material quantity is important to have accurate estimates. It’s not enough to say “windows”. How many? What size and type? What weight (in some cases)? These affect the cost and therefore need to be on your takeoff.
Sand and concrete are measured by volume. You should get an estimate of how much you’ll need from the architect and engineer.
Don’t skip this step and don’t guess! Use the architect and engineer’s expertise to guide you on what is realistic for your project.
If the values are off, you won’t create an accurate takeoff. Be as specific as possible
3. Make Concessions for Unforeseen Circumstances
It’s rare that any construction project is completely perfect. That is the nature of the beast.
There is always some margin of price fluctuations when planning any project.
This is where your expertise as an estimator comes in. What is happening in the market right now?
Is steel expensive? Is there a shortage of sand? How could this affect your budget calculations? What would be a reasonable percentage increase or decrease to add in line with material cost fluctuations at the moment?
4. Estimate the Cost per Material
The estimating process is the worst. Cost estimates are tough. Creating an accurate estimate is even tougher. This is why digital takeoff software can be helpful. They can help simplify the complex equations you need to do. Manual takeoffs are more labor-intensive.
Some things are easy because you have specialty contractor quotes you can draw from. If you need a double glazed window that is 25 x 35inches, you can ask a window supplier for a quote. Multiply that by the number of windows of that size. Hey presto, you have your window cost estimate.
But raw materials can be more complicated. Step 3 outlines that. The price of steel, sand, and lumber are changeable.
Estimators definitely have a tall order when it comes to takeoff accuracy.
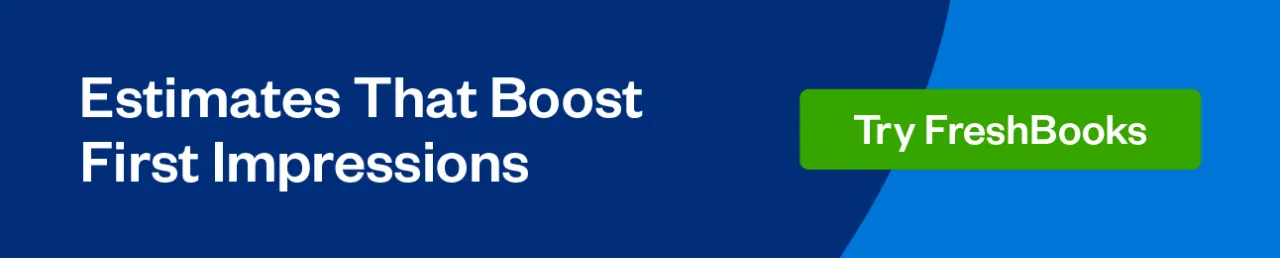
5.Review Your Construction Takeoff With the Client, Architect and Engineer
You rarely create a construction takeoff in a vacuum. It’s quite the feat to do it all yourself, but a second opinion is always welcome.
I recommend you review the final document with the engineers and architects. Make any tweaks if necessary before presenting the document to your client (if there is one). Work together as construction professionals to pool your collective industry knowledge.
After you have calculated your takeoff, you can add on labor costs to get the complete projected project spend.
Key Takeaways
Creating a construction material takeoff is simple in theory. Tough in practice.
Once you have the materials organized, you can use your expertise in the construction industry to guide your estimates.
For more guides like this on construction and other projects, head to our useful resource hub!
RELATED ARTICLES