What Is Inventory Carrying Cost & How to Calculate It?
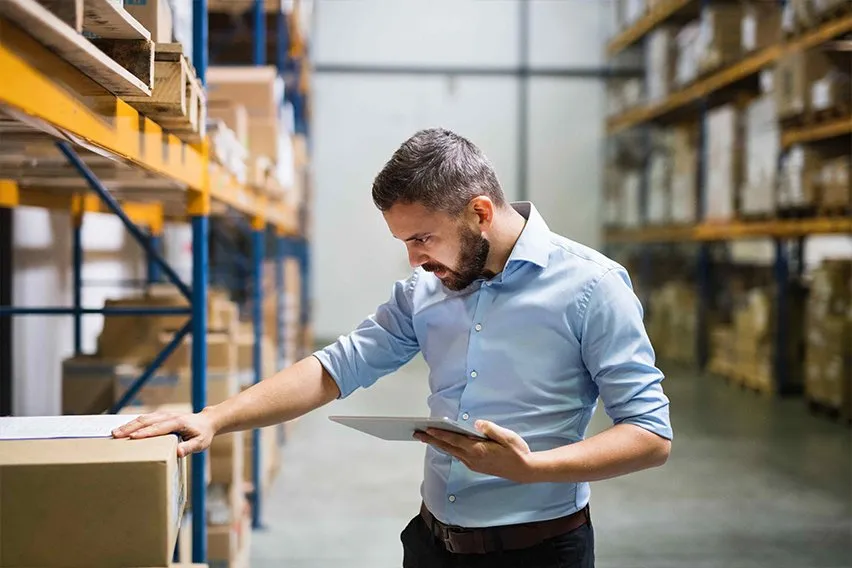
Inventory carrying costs have a lot to do with your profitability as a product-based small business. If your company maintains excess inventory, it will drain the business’s cash flow, making it difficult for you to meet running costs or break even. But, at the same time, your stock shouldn’t be too scanty or fall short of customer demands.
So what do you do? The hack is finding a balance.
This article will show you how to calculate inventory carrying costs to help you meet stock demand and supply for your business.
Here’s What We’ll Cover:
What Are Inventory Carrying Costs?
What Are the Types of Inventory?
What Are the Components of Inventory Carrying Costs?
How To Calculate Inventory Carrying Costs
What Do High Holding Costs Mean For Small Businesses?
4 Smart Ways to Bring Down Your Business Carrying Costs
More Inventory Management Resources for Business
What Are Inventory Carrying Costs?
Inventory carrying costs, or “holding costs”, refer to all the expenses a business incurs to stock and hold inventory over a period. The rule of thumb is these costs should account for 15% to 30% of a company’s total inventory value.
Common holding costs for businesses include quantifiable expenses like the money spent on settling taxes, employees’ salaries, warehousing, and insurance, as well as abstract expenses like opportunity costs, deterioration, and obsolescence.
Chances are, if you are a small business owner, then your current inventory is lower than that of a medium-sized or enterprise company. Inventory also varies according to industry, which means a medical supplies business might have higher operational costs than a bakery.
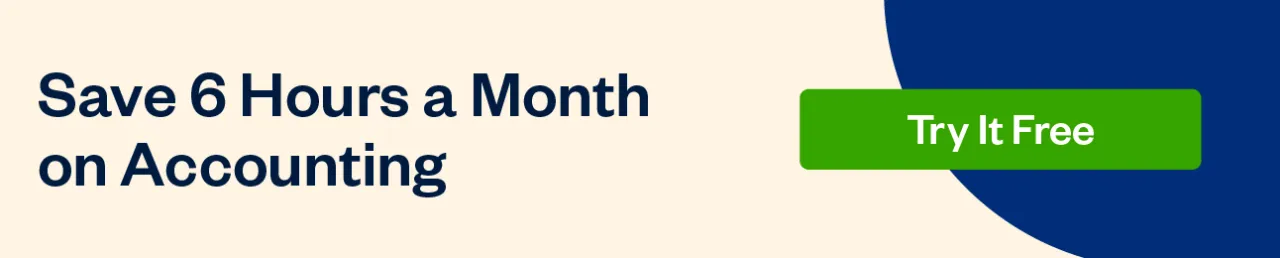
What Are the Types of Inventory?
Every production or manufacturing business is familiar with four types of inventory:
- Raw Materials
- Work In Progress
- Finished Goods
- Maintenance, Repair and Operating Inventory (MRO)
Raw Materials
Raw materials are the primary components used in a product’s manufacturing process. They include direct resources like flour for cake-making and indirect resources like the oil used to lubricate the oven.
A business can create its own raw materials (think of a farmer growing tomatoes for puree) or purchase them from other sources; most companies have a hybrid raw materials sourcing system.
Work in Progress
WIP inventory refers to all the items in ongoing production. It is everything in-between raw materials and finished products. So, if you run a bakery, the cake batter and unfinished pastries are part of your work-in-progress inventory.
Finished Goods
Finished goods are all the packed items that are ready to hit the market. You should think of them as short-term assets to be liquidated as soon as possible. The more time unsold products spend in your warehouse, the higher your inventory costs.
Maintenance, Repair and, Operating Inventory (MRO)
Everything you need to run your business falls under the maintenance, repair, and operating inventory. Here, consider cleaning supplies, gas, lubricants for your machines, and tools for equipment maintenance and repair.
What Are the Components of Inventory Carrying Costs?
To track holding costs accurately, business owners need to pay attention to the following;
- Capital Cost
- Storage Space Cost
- Inventory Service Cost
- Costs of Inventory Risks
Capital Costs
Capital costs refer to all the money plus interest invested in your business inventory. Here, think of monetary investments into fixed assets and the interest paid on a purchase.
Capital costs make up the bulk of your total inventory value, and it is represented as a percentage. For example, if a company’s capital cost is 25%, and its total inventory value is $100,000, its capital cost equals $25,000.
Storage Space Costs
All the funds that go into organizing and storing your stock fall under storage space costs. Top of mind in this category is the cost of buying or renting a warehouse, installing air conditioning, or paying for a heating system in your facility. In addition, variable storage costs cover utility and similar expenses.
Inventory Service Costs
Inventory service costs refer to expenses that help a company to manage its inventory effectively. For example, a business may opt for a subscription-based inventory management system for tracking its stock. In addition, companies incur service costs to meet up with the government’s regulations, like settling tax rates and insurance.
Inventory Risk Costs
Carrying business inventory comes with some uncertainties, and costs of inventory risks account for these uncertainties like:
- Shrinkage or inventory losses before the sale of an item to a customer
- Depreciation
- Obsolescence caused by product expiration
How To Calculate Inventory Carrying Costs
There are two ways to determine the holding costs for your business.
Formula 1
Inventory Carrying Cost Formula = Total Annual Inventory Value/4
Let’s say a business has an annual inventory value of $120,000. The inventory carrying cost is equal to $120,000/4 = $30,000. You can calculate your ending inventory using retail or gross profit.
This formula gives you a rough estimate of your business carrying cost. For a more accurate value, it is best to use the second calculation method.
Formula 2
Inventory Carrying Costs = (Inventory Holding Sum / Total Annual Inventory Value) x 100
Your inventory holding sum is an aggregation of the different inventory costs: Capital, storage, risks, and inventory services.
Here’s an example of how to use this cost formula:
Let’s say a small-sized engineering factory with a $100,000 inventory value incurred the following costs over the year;
Cost of Capital: $12,000
Storage Costs: $2,000
Service Costs: $3,500
Inventory Risk Costs: $4,500
First, add up these variables to get the inventory holding sum. That is;
$12,000 + $2,000 + $3,500 +$4,500 = $22,000
Next, divide this sum by the $100,000 annual inventory value and multiply the result by 100. So,
Inventory Carrying Cost = $22,000/$100,000 x 100 = 22%
What Do High Holding Costs Mean For Small Businesses?
High carrying costs could mean cost savings, on-time supplies, and increased customer satisfaction, especially for retail businesses like supermarkets and stores.
However, it could also lead to:
- Negative cash flow due to increased overhead costs
- Higher storage costs (warehouse rent)
- More insurance premiums
- Faster obsolescence and depreciation
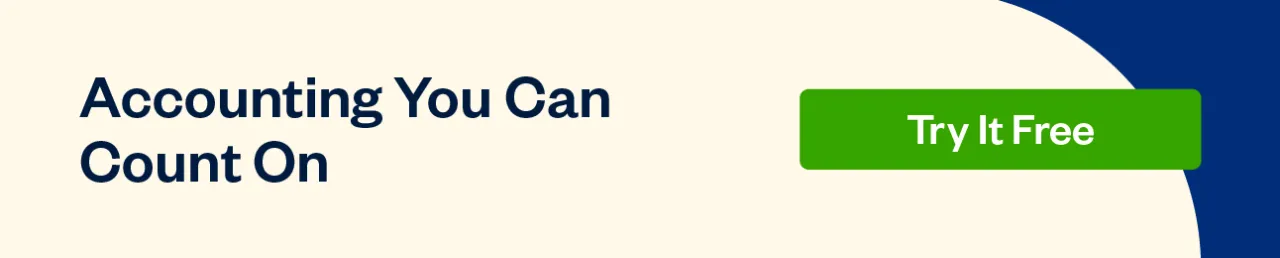
4 Smart Ways to Bring Down Your Business Carrying Costs
- Reduce your inventory holding
- Upgrade your warehouse
- Automate Your Inventory Management Process
- Eliminate Deadstock
Reduce Your Inventory Holding
The first thing you need to do is optimize your inventory level. This way, you wouldn’t have too little or too much stock at any point. Businesses need to balance demand and supply while improving their inventory turnover or sell-through rate.
It would be best if you look through your books and study your sales patterns. What items are in constant demand? Which ones take a longer time to sell out? When you have these data sets, you can plan your inventory holding quickly.
Upgrade Your Inventory Storage Space
Redesigning your warehouse space for storage efficiency helps you track your inventory fast. You can add new shelves to take more items; you can place similar items in containers or narrow the aisle in your facility.
Creating a compact storage facility for your inventory gives you a bird’s-eye view of all your stock. It may be hard to believe, but a simple tweak to your warehouse has the potential to lower tax costs, insurance premiums, capital, and depreciation.
Automate Your Inventory Management Process
Instead of recording your inventory on paper or a spreadsheet, choose a warehouse management system. If you own a small business, you can also use inventory management software for small businesses. For example, inventory tracking on FreshBooks means you can view, edit and review stockpiles right in your account. This modern approach to inventory management not only saves time but also helps in making informed decisions based on real-time data.
An inventory management software automatically updates your records and creates accurate demand and supply forecasts, giving you an accurate picture of your business stockpile levels.
Eliminate Deadstock
Having deadstock is similar to owning a white elephant—you spend lots of money on maintenance while it doesn’t bring any real value.
If you are stuck with stock, here are a few things you can do:
- Leverage the return policy and get your money back, if possible.
- Give it out to someone in need and enjoy generous tax savings.
- Turn them into customer freebies.
- Organize a clearance sale and see if anyone wants items in the stock.
Wrapping Up
Cash-strapped small businesses need to optimize their cost of inventory to free up revenue for everyday expenses. By monitoring carrying costs, companies can reduce unnecessary expenses and make data-driven business decisions.
More Inventory Management Resources for Business
- How to Calculate Ending Inventory
- What is a Perpetual Inventory System?
- Best Inventory Management Software for Small Businesses
RELATED ARTICLES