Make to Stock (MTS): Definition, Overview & How It Works
Depending on the type of business you operate and the industry that you are in, there can be different business strategies to implement. These strategies are going to vary and serve different purposes. But in the manufacturing industry, an effective strategy to use is make to stock (MTS).
So how exactly does it work and what are the biggest benefits? Keep reading to learn everything you need to know about make to stock and why it could be a solid strategy for your business.
Table of Contents
KEY TAKEAWAYS
- MTS is a production process where products get manufactured in advance and stored in anticipation of customer orders.
- Businesses that use MTS do not typically adjust their production based on customer demand.
- MTS can help businesses save on inventory costs, but it may result in stock-outs if demand unexpectedly spikes.
- MTS is suitable for products that have a relatively stable demand.
- MTS reduces the time needed to fulfill customer orders but can result in excessive inventory levels if demand changes.
What Is Make to Stock?
If you’re in manufacturing, chances are you’ve heard of make to stock (MTS) production. MTS is a production strategy where products get made without customer orders. In other words, products get made in advance and “stocked” until customers buy them.
The main goal of MTS is to have products available when customers want them. This usually means keeping finished goods inventory on hand. Suppose you know that demand for your product spikes during the holiday season. You would use MTS to ensure you have enough product in stock to meet that demand.
MTS contrasts with make to order (MTO) production. There, products are only manufactured after receiving customer orders.
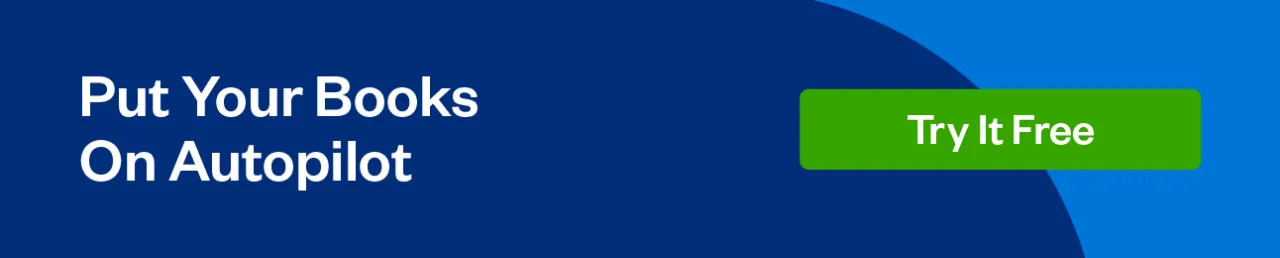
Example of MTS
A good example of MTS would be a company that manufactures t-shirts. The company knows that it generally sells more t-shirts in the summer than any other time of year. So it will produce a certain amount of t-shirts in advance and keep them in stock until customers purchase them.
In another example, a computer manufacturer may make a certain number of computers per month. It does this regardless of whether there are actual orders for them. The manufacturer may then sell the computers to distributors, who sell them to retailers. Retailers then sell the computers to customers.
For another example, a company that manufactures car parts may produce a certain number of engine parts per month. The company then sells the parts to automakers, who use them in the cars they produce.
Let’s look at one last example. A furniture company produces chairs. The company knows that demand for chairs spikes in the spring. So it manufactures a certain number of chairs in advance and keeps them in stock until customers buy them.
Advantages Of Make To Stock
There are several advantages of using the make-to-stock production schedule:
Reduced Lead Times
Since products get made without getting customer orders first, lead times decrease. This is because there’s no need to wait for customer orders before starting production.
Increased Efficiency
Make to stock production capacity is often more efficient than make to order production since it’s a simpler process with less steps.
Improved Forecasting
MTS can improve forecasting accuracy. This is since demand is more predictable when products are produced in advance and stocked until customers purchase them.
Reduced Costs
MTS can also help reduce costs. This is since inventory holding costs are lower than the cost of manufacturing products on an as-needed basis (i.e. make to order production).
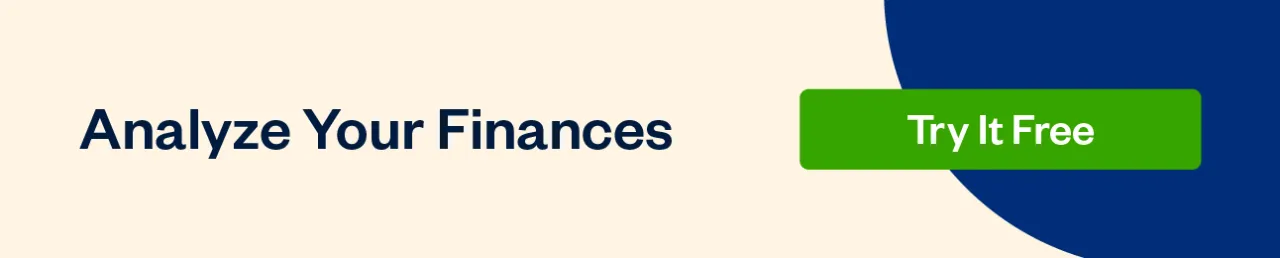
Disadvantages Of Make To Stock
There are also some disadvantages of using the make-to-stock production strategy:
High Inventory Levels
Since products are manufactured in advance, MTS can lead to high inventory levels. This can tie up working capital and increase storage costs.
Obsolescence
MTS can also lead to obsolescence if products become outdated before they’re purchased by customers. This can cause a company to lose money, especially if they deal in perishable goods.
And if the obsolete products are expensive to produce and cause the company significant losses, it can threaten the business.
Operations require a delicate balance to ensure products get sold on time. This isn’t always an easy endeavor. It’s why it’s so important to have experienced management.
Low Flexibility
MTS is not as flexible as other production strategies since it’s difficult to make changes once production has started. For example, if customer demand changes, it may not be possible to adjust production.
Make To Stock vs Make To Order
Make to stock and make to order are both production strategies, but they’re used in different ways. MTS is to have products available when customers want them. MTO is to manufacture products only after getting customer orders.
MTS can be more efficient than MTO since it’s a simpler process with fewer steps. MTS can also lead to high inventory levels. Obsolescence is also a concern if product demand becomes outdated before they’re purchased.
Also, MTO is more flexible since it allows for changes based on customer demand, but it can also be less efficient since it’s a more complex process.
In general, make-to-stock production is for companies with predictable demand. Make to order production is best suited for companies with less predictable demand.
What works best for you will depend on your company’s specific needs. For example, if you have a product with predictable demand, MTS may be the better option. However, MTO may be the better option if your product’s demand is less predictable.
Summary
Make to stock is a production strategy in which finished goods are produced in advance of customer orders. The goal of MTS is to maintain a stock of products that can be quickly and easily accessed by customers or retailers.
MTS is often used in manufacturing environments where there is high customer demand for a product. But there will be little variability in that demand. This strategy can help reduce manufacturing costs by allowing for the efficient use of resources. This helps minimize waste.
However, MTS can also lead to inventory issues if demand for a product unexpectedly increases or decreases. In these cases, manufacturers may find themselves with too much or too little stock, which can lead to lost sales or wasted resources.
It’s important to have a strong planning strategy in place. You should account for this throughout the planning process. Anticipated consumer demand can ensure that you meet demands each production period.
You may have to order more raw materials, but that also means you’ll sell more.
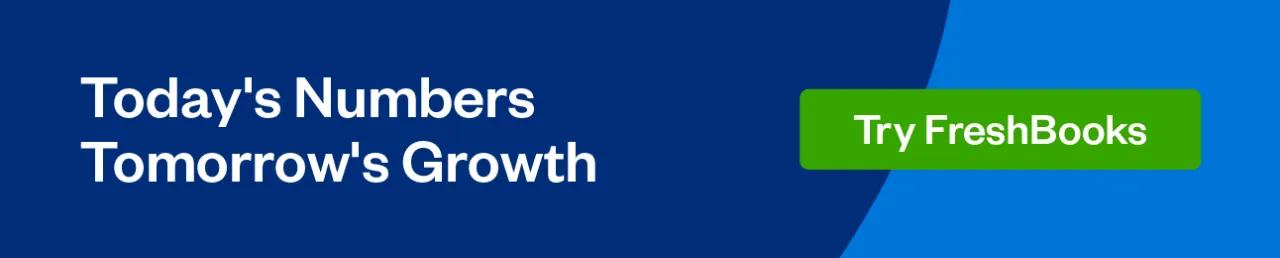
Make To Stock FAQs
There are several reasons why. Some companies might use make to stock production to reduce lead times or increase efficiency. Others may use it to improve forecasting accuracy.
Some advantages of using this strategy include reduced lead times and increased efficiency.
Some disadvantages include high inventory levels and obsolescence.
Make to stock and make to order are both production strategies, but they’re used in different ways. MTS is used to have products available when customers want them, while MTO is used to manufacture products only after customer orders.
The steps usually include forecasting demand, setting inventory levels, and scheduling production.
Make to stock production is often used for products with predictable demand, such as fast-moving consumer goods.
Share: